Calculation Spreadsheet for the Implementation of Photovoltaic Plants Read More »
Elétrica
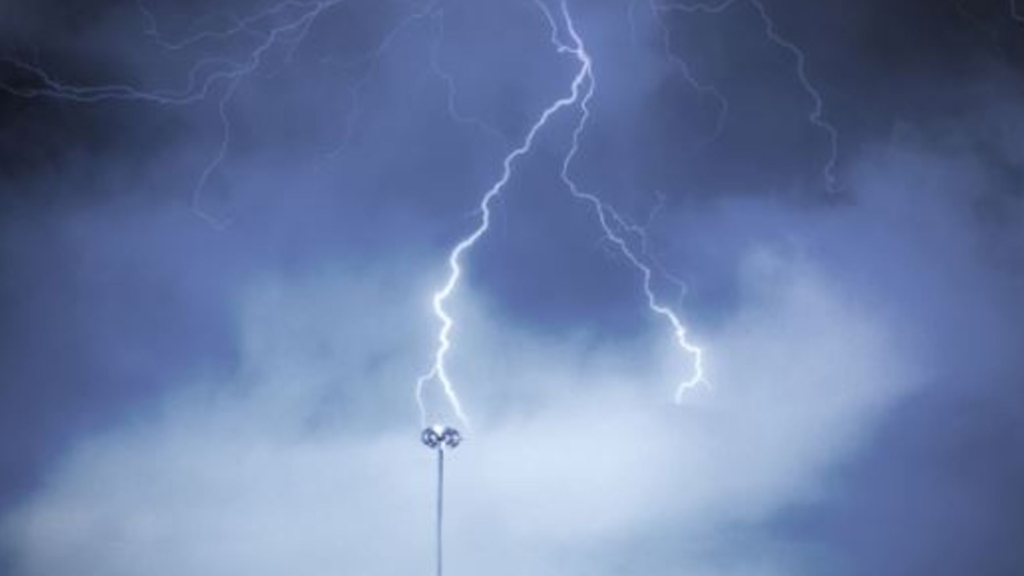
Lightning strikes represent a significant threat to buildings, power transmission lines, and electronic equipment. Implementing a robust Lightning Protection System (LPS) is essential to minimize damage caused by these events. In this article, we explore the components, methods, and best practices to ensure the safety of your installations.
What Are Lightning Strikes?
Lightning strikes can be categorized as either direct or indirect:
- Direct Strikes: These occur when lightning directly impacts a structure, such as a building or power transmission line. A robust LPS is required to intercept and safely conduct the lightning’s energy to the ground.
- Indirect Strikes: These are surges induced in electrical systems due to the proximity of a direct strike. Though less visible, these surges can significantly damage sensitive electronic equipment.
Essential Components of an LPS
An effective Lightning Protection System consists of several key elements, each playing a critical role in ensuring the safety of the structure:
- Air Terminals: These are the first line of defense, including lightning rods, masts, or conductor cables that intercept lightning strikes.
- Down Conductors: These are cables that connect the air terminals to the grounding system, guiding the lightning’s energy safely to the earth.
- Grounding System: This disperses the lightning’s energy into the earth, minimizing the risk of damage to the structure and its equipment.
- Bonding and Equipotentialization: This integrates the metallic components of a building with the grounding system to prevent hazardous voltage differentials and improve overall safety.
Methods of Protection: Choosing the Best for Your Structure
In the United States, lightning protection standards such as NFPA 780 and UL 96A, and in the UK, standards like BS EN 62305, provide guidelines for LPS design. Common methods include:
Rolling Sphere Method (RSM)
The RSM determines protected areas using a conceptual “rolling sphere” to simulate the trajectory of a lightning strike.
- How It Works:
- A sphere with a defined radius (based on lightning intensity) is rolled over the structure. Any point touched by the sphere is at risk and requires protection.
- Protected areas are those shielded by air terminals or other protective elements.
- A sphere with a defined radius (based on lightning intensity) is rolled over the structure. Any point touched by the sphere is at risk and requires protection.
- Applications: This method is ideal for large or complex structures, such as tall buildings and industrial facilities.
Franklin Rod Method
Also known as the “traditional lightning rod method,” this approach simplifies protection for smaller structures.
- How It Works:
- A cone of protection is defined by an angle extending from the lightning rod to the ground, forming a protective zone around the structure.
- Suitable for residences, small factories, or storage facilities.
- A cone of protection is defined by an angle extending from the lightning rod to the ground, forming a protective zone around the structure.
- Benefits:
- Easy to implement.
- Cost-effective for smaller buildings.
- Easy to implement.
Faraday Cage Method
This approach is based on Faraday’s principle, using a grid of conductors to protect large areas such as warehouses, factories, or skyscrapers.
- How It Works:
- A mesh of conductors is installed over and around the structure, intercepting strikes before they reach the interior.
- Metallic elements like window frames and railings are bonded to the grid, ensuring any lightning current is safely conducted to the ground.
- A mesh of conductors is installed over and around the structure, intercepting strikes before they reach the interior.
- Benefits:
- Comprehensive protection for large or high-risk structures.
- Effective for buildings with extensive metallic exteriors.
- Comprehensive protection for large or high-risk structures.
Importance of Grounding and Electrical Continuity
Grounding is a critical component of any LPS. According to NFPA 780 and BS EN 62305, the grounding resistance should ideally be below 10 ohms. Proper grounding ensures efficient dissipation of lightning energy, while regular testing of electrical continuity ensures all conductive elements function effectively in a lightning event.
FAQ: Lightning Protection Systems
- What is an LPS?
An LPS is a set of devices and methods designed to protect buildings and facilities from lightning strikes by safely conducting the energy to the ground. - What’s the difference between direct and indirect strikes?
Direct strikes impact a structure directly, while indirect strikes involve surges induced in electrical systems by nearby lightning. - What role does grounding play in an LPS?
Grounding disperses intercepted lightning energy into the earth, reducing risks to the structure and equipment. - How does the Rolling Sphere Method work?
It uses a virtual sphere to identify unprotected areas on a structure, ensuring adequate coverage by air terminals. - When should the Faraday Cage Method be used?
This method is ideal for large industrial facilities or buildings with extensive exposed areas.
Conclusion
Implementing a compliant and effective Lightning Protection System is essential to safeguard structures against lightning strikes. Adhering to standards like NFPA 780 or BS EN 62305 ensures both safety and compliance, minimizing risks and preserving the integrity of your assets.
If you liked this article, consider sharing it on social media, this will help to spread knowledge, leave your comment below so we can know your opinion.
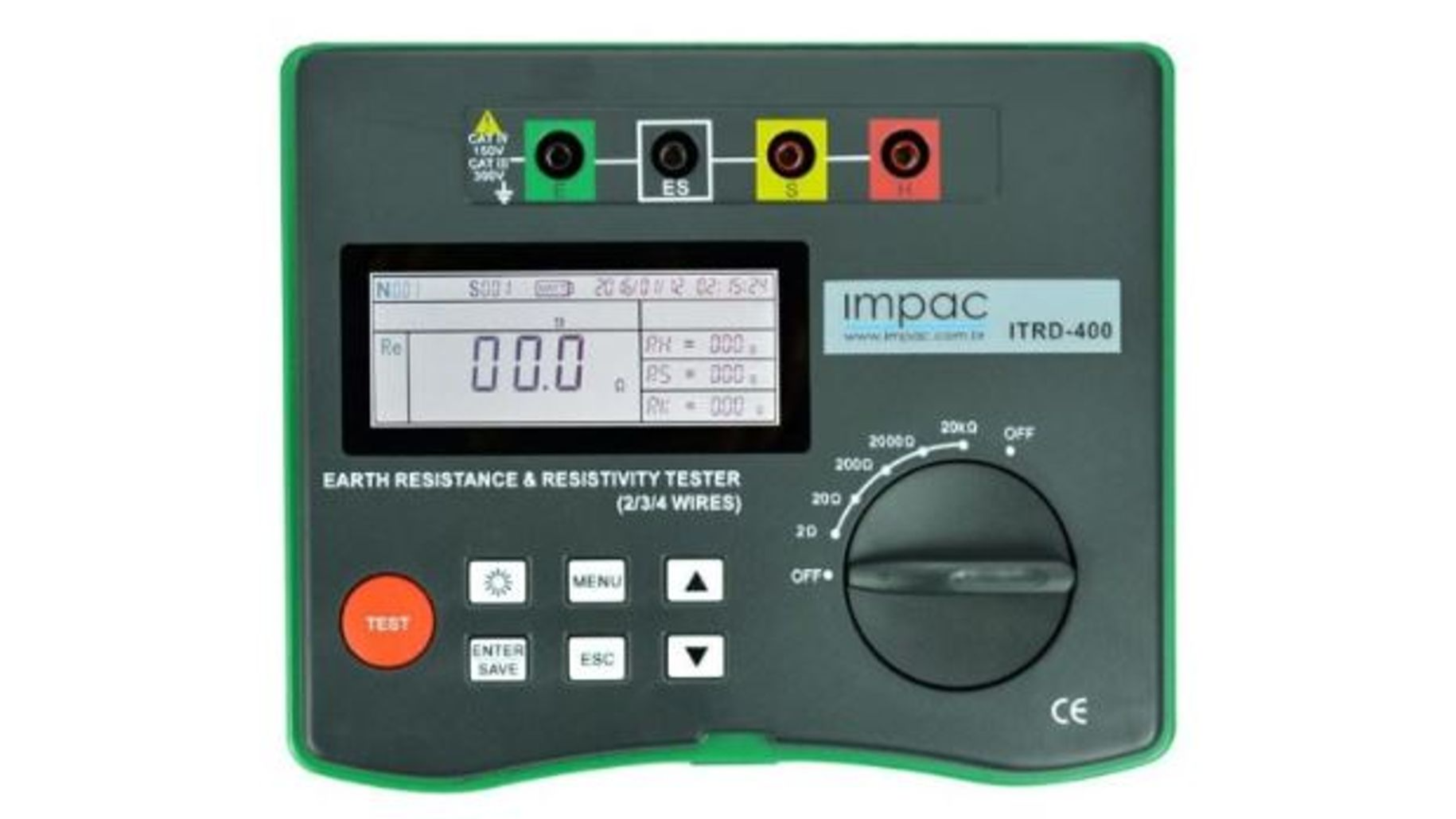
An Earth Resistance Tester is a crucial instrument used by engineers and technicians to measure soil resistance to electrical discharges. This measurement evaluates the efficiency of grounding systems, ensuring they function properly and provide safety for equipment and people.
How Does an Earth Resistance Tester Work?
Grounding is essential in electrical installations to prevent power surges or overloads from damaging equipment. When analyzing a grounding system, the impedance values of electrodes are assessed according to electrical codes and engineering standards.
The Earth Resistance Tester measures this impedance: the lower the impedance, the better the grounding performance. Ideally, grounding resistance should be below 10 Ohms, while values above 30 Ohms may pose risks.
Types of Earth Resistance Testers
Different applications and precision requirements dictate the type of tester to use. The main types include:
1. Three-Wire Earth Resistance Tester
This traditional tester measures soil resistance by evaluating the voltage along the path of the electric current back to the grounding electrode. It is ideal for open systems and industrial environments.
- Features: Measures ground resistance with high accuracy using three electrodes.
- Applications: Suitable for isolated grounding systems.
2. Clamp-On Earth Resistance Tester
This type measures resistance in closed circuits without disconnecting the ground system, making it practical and efficient for quick maintenance.
- Features: Measures resistance through induction without auxiliary electrodes.
- Applications: Ideal for substations and electrical panels.
3. Digital Earth Resistance Tester
Advanced models offering precise measurements with features like data storage and graphical analysis.
- Features: High precision, digital display, and advanced options.
- Applications: Used in complex industrial systems.
4. Portable Earth Resistance Tester
Compact and lightweight, this tester is ideal for fieldwork requiring mobility.
- Features: Easy to transport without compromising accuracy.
- Applications: Residential and small-scale commercial projects.
5. High-Frequency Earth Resistance Tester
Used for measuring resistance at higher frequencies, suitable for specific installations such as communication systems.
- Features: Operates at higher frequencies.
- Applications: Lightning protection systems (SPDA).
Steps for Measuring Ground Resistance
- Position the Electrodes:
- Fixed Electrode: Acts as a reference point (ground rod).
- Current Electrode: Positioned at least three times the length of the fixed rod.
- Voltage Electrode: Placed 62% of the distance between the fixed and current electrodes.
- Take Measurements:
- Connect the tester to the electrodes.
- Measure and compare the resistance values with established standards.
- Improve Ground Resistance:
- If resistance is too high, increase the grounding mesh by adding interconnected rods.
Precautions When Using an Earth Resistance Tester
- Ensure batteries are correctly installed.
- Use the appropriate testing function.
- Avoid active electrical circuits.
- Protect the tester from prolonged sun exposure.
- Remove batteries when not in use.
- Wear safety equipment such as insulated gloves and shoes.
Summary of Earth Resistance Testers
Type | Main Application | Notable Advantage |
---|---|---|
Three-Wire Tester | Isolated systems | High accuracy in complex systems |
Clamp-On Tester | Maintenance and inspections | Measures without disconnection |
Digital Tester | Complex industrial installations | Advanced features |
Portable Tester | Field measurements | Compact and transportable |
High-Frequency Tester | SPDA and communication systems | Operates at high frequencies |
Conclusion
The Earth Resistance Tester is indispensable for ensuring electrical safety in residential, industrial, and commercial installations. Proper use and maintenance prevent equipment damage and enhance safety for people.
FAQ
- What is an Earth Resistance Tester?
- It is an instrument used to measure soil resistance and evaluate the efficiency of grounding systems.
- Why is grounding important?
- Grounding directs leakage currents to the ground, preventing damage and ensuring safety.
- How does the tester measure soil resistance?
- It assesses soil’s ability to dissipate electrical currents using sensors.
- What is the ideal grounding resistance?
- Generally, values below 10 Ohms are safe, depending on technical standards.
- Who should use an Earth Resistance Tester?
- Qualified professionals, such as electrical engineers, should use it for accurate and safe measurements.
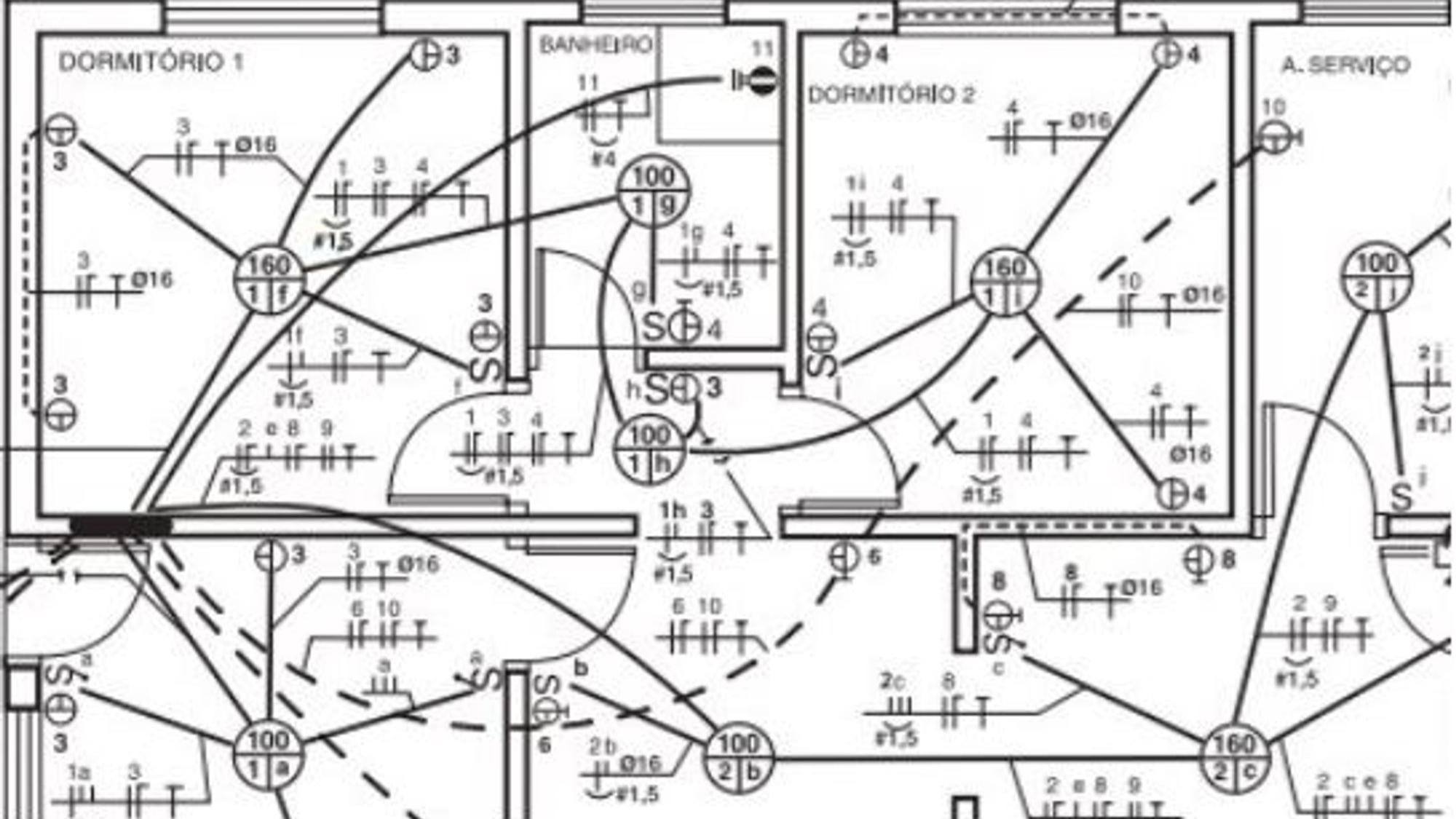
Creating electrical projects is a crucial process to ensure safety, efficiency, and compliance with regulations, especially when conducted according to current technical standards such as the National Electrical Code (NEC) in the United States and the BS 7671 (IET Wiring Regulations) in the United Kingdom. In this article, we will explore in detail each step of the process, from component sizing to voltage drop verification, ensuring you can design a robust electrical project that adheres to these regulations.
1. The Importance of Electrical Projects and Compliance with Standards
Well-designed electrical projects, in compliance with standards such as the NEC and BS 7671, are essential to prevent accidents, optimize energy use, and ensure installations meet regulatory requirements. Following these standards is critical for the safety and longevity of electrical systems.
Fundamental Steps in Electrical Project Design
2. Sizing and Location of Components
The NEC and BS 7671 provide guidelines for the sizing and location of components, such as light points, outlets, distribution boards, switches, and doorbell buttons. These components must adhere to specific criteria to ensure safety and functionality. It is essential to position each component strategically, based on the intended use of spaces, ensuring efficient electrical distribution.
3. Electrical Conduit Design
The design and installation of electrical conduit networks must be planned to safely and efficiently route electrical wires throughout environments. Careful planning of this network helps avoid issues such as overloads and facilitates future maintenance. The NEC and BS 7671 specify materials and installation methods to ensure the durability and safety of the system.
4. Load Distribution across Circuits
The distribution of electrical loads across separate circuits, such as lighting, outlets, and high-power equipment, is recommended by the NEC and BS 7671. This division enables balanced energy demand distribution, preventing overloads and enhancing system safety. The standards also set current limits for each circuit type, ensuring the system is properly sized.
5. Load Panel Organization and Single-Line Diagram
The load panel and single-line diagram should be organized clearly and in detail, to facilitate system understanding and maintenance. The load panel must indicate all loads connected to the system, while the single-line diagram provides a graphical representation of the energy distribution.
6. Sizing of Conduits and Wiring
The standards specify minimum conduit diameters and wire gauges based on the expected electrical current and installation conditions. Adhering to these specifications prevents issues like overheating and ensures system durability.
7. Voltage Drop Verification
The NEC and BS 7671 set limits for the maximum allowable voltage drop in electrical circuits. Verifying the voltage drop is essential to ensure that all consumption points receive voltage within acceptable parameters. To do this, the standards recommend using minimum wire gauges, such as 1.5 mm² for lighting circuits and 2.5 mm² for outlet circuits, ensuring system compliance and safety.
8. Sizing of Feeders
The sizing of feeders should be done based on the total energy demand, considering voltage drop limits and the specifications in the NEC and BS 7671. The standards provide guidance on selecting conductors and sizing criteria to ensure that feeders meet safety and efficiency requirements.
9. Organization of the Main Load Panel
The NEC and BS 7671 require that the main load panel be organized to separate loads by type, such as lighting, outlets, showers, air conditioning, and motors. This organization simplifies energy distribution management and ensures that each load type is powered correctly, in compliance with standard limits.
10. Diversity Factor Calculation
The diversity factor, as outlined in the NEC and BS 7671, is used to optimize the sizing of electrical systems, considering that not all loads will be used simultaneously. The standards provide guidelines on how to calculate the diversity factor for different types of buildings and installations, ensuring efficient electrical system sizing without overloading components.
11. Sizing of the General Service Entrance
The general service entrance should be sized based on total demand, considering NEC and BS 7671 specifications. This includes selecting the appropriate cabling, protective devices, and, if necessary, installing a substation.
FAQ
1. Why is it important to follow the NEC and BS 7671 in electrical project design?
Following the NEC and BS 7671 is crucial to ensure the safety of electrical installations, prevent accidents, and ensure that the system complies with current regulations.
2. What are the NEC and BS 7671, and what do they cover?
The NEC (National Electrical Code) is a U.S. standard that governs electrical installations, while BS 7671 (IET Wiring Regulations) is the UK standard for wiring and electrical installations. Both standards cover guidelines from component sizing to safety and maintenance criteria.
3. How do the NEC and BS 7671 guide the sizing of electrical components?
Both standards provide specific criteria for sizing and positioning components, such as conduits, wiring, and distribution boards, ensuring the safety and efficiency of installations.
4. What are the voltage drop limits established by the NEC and BS 7671?
The NEC allows a maximum voltage drop of 3% for branch circuits and feeders, while BS 7671 recommends a maximum drop of 4% for circuits in normal installations, ensuring that voltage at consumption points remains within proper limits.
5. How do the NEC and BS 7671 address the diversity factor in electrical system sizing?
Both standards offer guidance on calculating the diversity factor, which helps optimize electrical system sizing by considering the non-simultaneous use of loads, ensuring efficiency and safety.
If you liked this article, consider sharing it on social media, this will help to spread knowledge, leave your comment below so we can know your opinion.
The table of Rated Current for Cylindrical Fuses and Bases provides information on the current capacities of cylindrical fuses, which are critical components in electrical systems for protection against overcurrents.
Cylindrical Fuses Utilization Category gG/aM | |||||
---|---|---|---|---|---|
Dim. (mm) | Rated Current (A) | Dim. (mm) | Rated Current (A) | Dim. (mm) | Rated Current (A) |
10x38 | 1 | 14x51 | 2 | 22x58 | 8 |
10x38 | 2 | 14x51 | 4 | 22x58 | 10 |
10x38 | 4 | 14x51 | 6 | 22x58 | 12 |
10x38 | 6 | 14x51 | 8 | 22x58 | 16 |
10x38 | 8 | 14x51 | 10 | 22x58 | 20 |
10x38 | 10 | 14x51 | 12 | 22x58 | 25 |
10x38 | 12 | 14x51 | 16 | 22x58 | 32 |
10x38 | 16 | 14x51 | 20 | 22x58 | 40 |
10x38 | 20 | 14x51 | 25 | 22x58 | 50 |
10x38 | 25 | 14x51 | 32 | 22x58 | 63 |
10x38 | 32 | 14x51 | 40 | 22x58 | 80 |
14x51 | 50 | 22x58 | 100 |
Bases for Cylindrical Fuses | |||
---|---|---|---|
Dim. (mm) | Rated Current (A) | Number of Poles | Conductor Cross-Section (mm²) |
10x38 | 32 | 1 | 2,5 a 16 |
10x38 | 32 | 2 | 2,5 a 16 |
10x38 | 32 | 3 | 2,5 a 16 |
10x38 | 32 | 3+N | 2,5 a 16 |
14X51 | 50 | 1 | 2,5 a 25 |
14X51 | 50 | 2 | 2,5 a 25 |
14X51 | 50 | 3 | 2,5 a 25 |
14X51 | 50 | 3+N | 2,5 a 25 |
22x58 | 100 | 1 | 4 a 50 |
22x58 | 100 | 2 | 4 a 50 |
22x58 | 100 | 3 | 4 a 50 |
22x58 | 100 | 3+N | 4 a 50 |
If you enjoyed this article, consider sharing it on social media. By doing so, you’ll help spread knowledge. Leave your comment below to let us know your opinion.
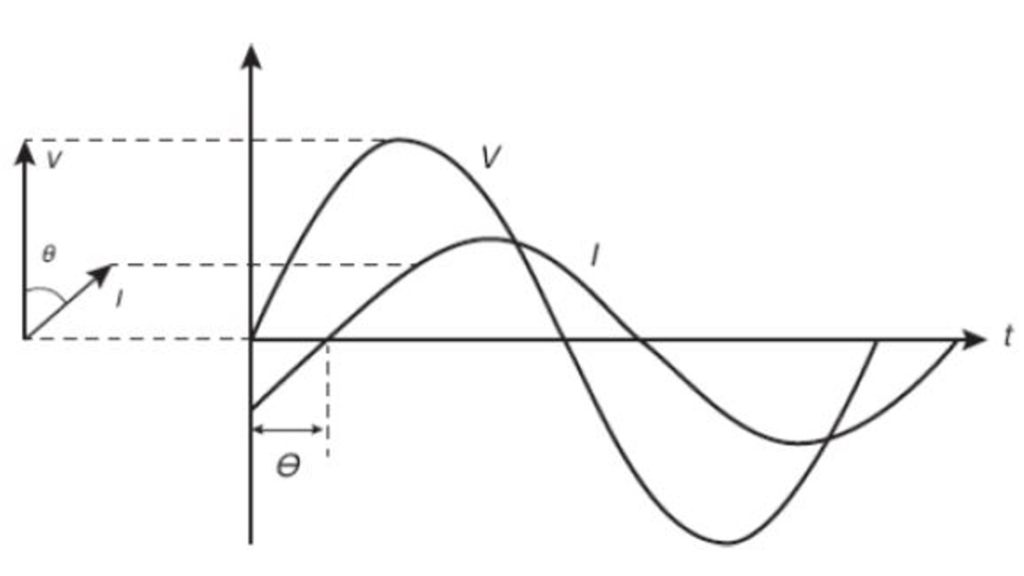
The power factor (PF) is a crucial concept in electrical systems, representing the relationship between active power, which performs useful work, and apparent power, which is the vector combination of active and reactive power. Understanding and managing power factor is essential for optimizing the efficiency of electrical systems and avoiding issues such as energy losses and conductor overheating.
What is Power Factor?
Power factor is defined as the cosine of the phase angle between current and voltage in a circuit. For single-phase AC circuits, it can be calculated using the formula:
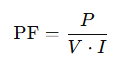
Where:
- P is the power in watts (W),
- V is the voltage in volts (V),
- I is the current in amperes (A).
For three-phase systems, the formula is adjusted to consider the three phases:
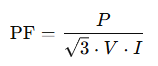
The power factor value ranges from 0 to 1 (or 0% to 100% in percentage terms), where:
- 0 indicates pure inductive or capacitive loads (a theoretical situation since practical circuits always have some resistance),
- 1 indicates a purely resistive circuit.
Types of Power
Electrical systems deal with three main types of power:
- Active Power (P): The power that performs useful work, such as driving motors or heating elements.
- Reactive Power (Q): The power that oscillates between the generator and the load due to inductive and capacitive components, without performing useful work.
- Apparent Power (S): The vector sum of active and reactive power, representing the total power supplied to the circuit.
These powers are represented in a power triangle, where the power factor is the cosine of the phase angle.
Practical Example
Consider a three-phase motor operating at 220 volts, drawing 25 amperes per phase with a power factor of 80%. The power supplied by the system can be calculated as:

This calculation illustrates how power factor directly affects the total power required by the system.
Impacts of a Low Power Factor
A low power factor, typically below 0.92, can lead to several issues in an electrical installation, including:
- Conductor Overheating: Increased current is needed to deliver the same active power, which can cause overheating and equipment failure.
- Higher Energy Bills: Utilities often impose penalties for low power factor, as it indicates reduced energy efficiency.
To correct power factor, capacitors are commonly installed in parallel with inductive loads. This reduces reactive power, increases power factor, and improves system efficiency.
Importance of Power Factor in Electrical Engineering
Managing power factor is vital for electrical engineers aiming to optimize energy efficiency. A high power factor not only reduces operating costs but also extends equipment lifespan and enhances system stability. Therefore, power factor should be a key consideration in electrical design, maintenance, and operation of installations.
FAQ about Power Factor
1. What is power factor?
Power factor (PF) is a measure of how efficiently electrical power is used. It is defined as the ratio of active power (used for useful work) to apparent power (total power supplied to the system).
2. What is the difference between active, reactive, and apparent power?
- Active Power (P): The portion of power that performs useful work, such as running motors or heating resistors.
- Reactive Power (Q): Power that oscillates between the source and load due to inductive or capacitive elements, not contributing to useful work.
- Apparent Power (S): The total power supplied to the circuit, combining active and reactive power vectorially.
3. What causes a low power factor?
A low power factor is usually caused by inductive loads such as motors, transformers, and reactors, which require reactive power to create magnetic fields necessary for their operation.
4. What are the consequences of a low power factor?
- Increased energy losses in the system;
- Overloading of cables, transformers, and other equipment;
- Excessive heating of conductors;
- Financial penalties from utility companies for inefficient power use.
5. How can power factor be corrected?
Power factor correction is typically achieved by installing capacitors parallel to inductive loads. Capacitors provide reactive power locally, reducing the demand on the power supply and improving efficiency.
6. What is the ideal power factor?
An ideal power factor is close to 1 (or 100%), indicating that all supplied power is being effectively used for productive work.
7. Why do utility companies charge penalties for low power factor?
Utilities charge penalties because a low power factor increases the current in the system, requiring larger infrastructure and causing greater energy losses.
8. What is the difference between individual and centralized power factor correction?
- Individual Correction: Capacitors are installed near specific loads, such as motors, to address localized issues.
- Centralized Correction: A capacitor bank is installed at the main distribution board to correct the power factor for the entire system.
9. What equipment can help monitor power factor?
Power meters with PF monitoring, protection relays, and SCADA (Supervisory Control and Data Acquisition) systems are commonly used to track and manage power factor.
10. Does power factor affect the lifespan of equipment?
Yes, a low power factor can cause overloading and heating of equipment, leading to reduced lifespan and potential failures.
11. How do capacitors improve power factor?
Capacitors counteract the inductive effects of loads by supplying reactive power locally, reducing the overall reactive power demand on the system and improving the power factor.
12. What is a power factor penalty, and how is it calculated?
A power factor penalty is a surcharge imposed by utility companies when the power factor falls below a certain threshold, typically 0.92 or 0.95. The penalty is calculated based on the additional apparent power required due to the inefficiency.
13. How does power factor impact energy costs?
A low power factor results in higher apparent power demand, increasing the utility’s delivery capacity and operational costs, which are often passed on to consumers through penalties or higher rates.
14. Can renewable energy systems impact power factor?
Yes, systems like solar inverters or wind turbines may influence power factor, especially if not properly designed or synchronized with the grid. Advanced inverters with power factor correction capabilities can mitigate these effects.
15. Is power factor important for residential installations?
While power factor is more critical in industrial and commercial settings, improving it in residential systems can still help reduce energy waste and optimize the performance of household appliances.
If you liked this article, consider sharing it on social media, this will help to spread knowledge, leave your comment below so we can know your opinion.
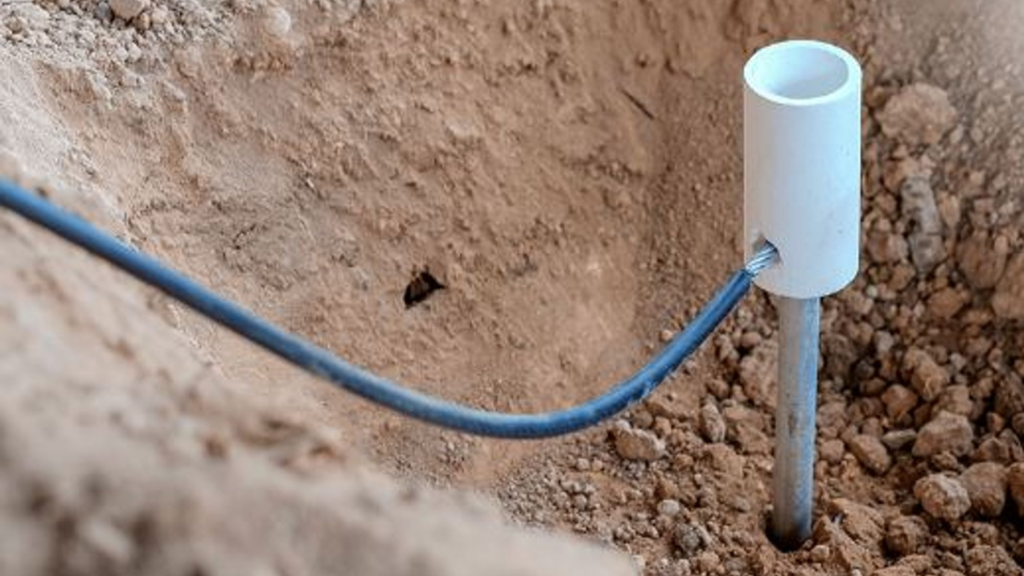
Grounding is an essential part of electrical installations, ensuring a safe connection between electrical structures or systems and the earth. This connection allows various types of electrical currents to safely flow into the ground, minimizing risks to people, animals, and equipment. The main currents dissipated to the ground include:
- Lightning Currents: Caused by direct or indirect lightning strikes on the electrical system.
- Electrostatic Discharge Currents: Resulting from accumulated charges on insulating materials.
- Currents from Filters, Surge Protectors, and Line Arresters: Generated by devices protecting against overvoltages.
- Fault Currents to Ground: Arising from short circuits or insulation failures affecting the system.
Basic Types of Grounding in Electrical Installations
Functional Grounding
- Description: Establishes a connection to ground for one of the system conductors, typically the neutral.
- Purpose: Ensures proper and safe system operation.
Protective Grounding
- Description: Connects metallic parts of equipment and non-current-carrying conductive parts to the ground.
- Purpose: Protects against electric shocks, especially during fault conditions.
Working Grounding
- Description: Provides a temporary connection to the ground for parts of the system during maintenance.
- Purpose: Ensures worker safety during system servicing.
Standards for Grounding
In the United States and the United Kingdom, grounding systems for low voltage installations follow stringent standards:
- United States:
- National Electrical Code (NEC) 2023: Defines grounding and bonding requirements to ensure safety and functionality.
- IEEE 80: Provides guidelines for grounding design in substations and industrial settings.
- National Electrical Code (NEC) 2023: Defines grounding and bonding requirements to ensure safety and functionality.
- United Kingdom:
- BS 7671:2018 (18th Edition of the IET Wiring Regulations): Establishes grounding requirements for all electrical installations.
- BS EN 62305: Addresses protection against lightning strikes, complementing the grounding requirements.
- BS 7671:2018 (18th Edition of the IET Wiring Regulations): Establishes grounding requirements for all electrical installations.
Elements of a Grounding System
A low-voltage grounding system comprises the following components:
- Protective Conductors: Connect equipment casings to the grounding system.
- Equipotential Bonding Conductors: Ensure uniform potential throughout the installation.
- Ground Electrodes: Provide direct contact with the earth.
Integration of Grounding Systems
In industrial and commercial settings, integrating various grounding subsystems enhances performance and safety. Key considerations include:
- Neutrals and Protective Conductors: Connected to the power distribution system.
- Lightning Protection Grounding: For handling lightning-induced currents.
- Signal Grounding and “Reference Planes”: Vital for sensitive electronic equipment like laboratory instruments and data centers.
- Structural Grounding: Includes metallic frameworks, pipes, and control panels.
Common Grounding Schemes
Electrical systems are classified using codes (e.g., TN, TT, IT), which dictate the grounding method and protective measures:
TN System
- One point of the power supply is grounded.
- Variants:
- TNS: Separate neutral (N) and protective earth (PE) conductors throughout the installation.
- TNCS: Combines neutral and protective functions into a single conductor (PEN) for part of the installation.
- TNC: Combines neutral and protective functions in one conductor across the entire installation.
- TNS: Separate neutral (N) and protective earth (PE) conductors throughout the installation.
TT System
- Equipment masses are grounded independently of the power supply ground.
- Key Feature: Mandatory use of Residual Current Devices (RCDs) for effective fault protection.
IT System
- No direct connection of the power supply to the ground (or connected via high impedance).
- Commonly used in industrial processes requiring uninterrupted power. Continuous fault monitoring is essential.
Importance of Impedance and Fault Clearing Time
To ensure effective fault protection, the impedance of the fault current path (Zs) and the operating current of the protective device (Ia) must meet the condition:
Zs × Ia ≤ U0, where U0 is the nominal phase-to-ground voltage.
This guarantees the protective device (e.g., a circuit breaker) will disconnect the circuit within the specified time, minimizing exposure to dangerous touch voltages.
Risk Assessment and Environmental Factors
Grounding standards, such as NEC and BS 7671, classify risk based on environmental conditions and human electrical resistance. This determines additional protective measures required for specific scenarios, like wet environments or medical facilities.
Conclusion
Grounding is a cornerstone of electrical safety. Understanding grounding schemes, impedance considerations, and risk classifications is critical for designing and maintaining safe electrical systems. Compliance with standards such as NEC and BS 7671 ensures installations are safe, efficient, and free from electrical hazards.
FAQ on Grounding Systems
- What is grounding, and why is it important?
Grounding connects exposed metallic parts to the earth, preventing electric shock and equipment damage during faults. - What are the main grounding schemes?
The TN, TT, and IT schemes define how grounding and fault protection are implemented in electrical systems. - When should RCDs be used?
RCDs are mandatory in TT systems and highly recommended in TN systems to ensure fault protection. - What is the purpose of impedance in grounding?
Impedance ensures the protective devices operate effectively by controlling the fault current’s path and magnitude. - How do environmental factors affect grounding?
Conditions like humidity, floor conductivity, and the presence of conductive surfaces influence grounding design and protective measures.
If you liked this article, consider sharing it on social media, this will help to spread knowledge, leave your comment below so we can know your opinion.
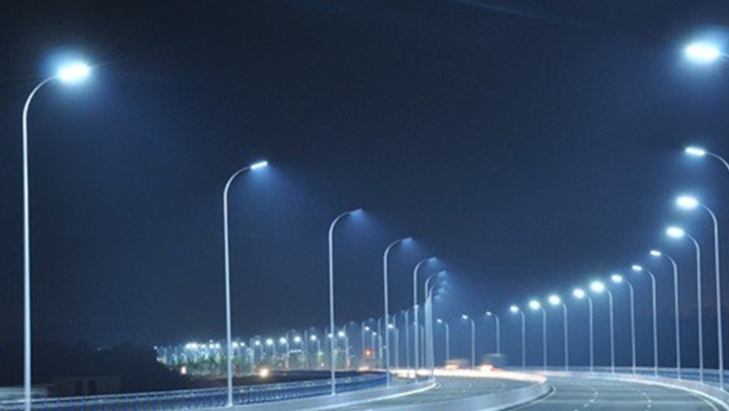
To develop efficient lighting projects, understanding the fundamental lighting quantities is essential. These quantities are based on definitions established by standards such as ISO 8995-1 and by organizations like the Illuminating Engineering Society (IES) in the United States and the British Standards Institution (BSI) in the United Kingdom. Below, we explore the key concepts governing light and its application in lighting design.
Light and Wavelength
Light is the portion of radiant energy visible to the human eye, perceived through the stimulation of the retina. The electromagnetic radiation detectable by the human eye spans wavelengths from 380 to 760 nanometers (nm). A nanometer equals one billionth of a meter.
The wavelength (λ) is the distance between corresponding points of consecutive waves, usually peaks, in a graph of space versus amplitude. The product of wavelength and frequency (f) equals the speed of light (c), which is constant at approximately 186,282 miles per second (or 3 × 10⁸ m/s).
Color of Light
The color of light is determined by its wavelength. Violet light has the shortest visible wavelength (380–450 nm), while red light has the longest (640–760 nm). The visible spectrum, illustrated below, shows that yellow light at 555 nm provides the greatest visual sensitivity.
Lighting Quantities
Luminous Intensity (Candela – cd)
Luminous intensity measures the amount of light emitted by a source in a specific direction. It is defined as the luminous intensity, perpendicular to a flat surface of 1/600,000 square meters of a black body at the temperature of platinum’s freezing point, under 1 atmospheric pressure.
This measure is critical for directional lighting, such as spotlights and reflectors, where intensity in a specific direction is prioritized over general lighting.
Luminous Flux (Lumen – lm)
Luminous flux represents the total amount of light emitted by a source in all directions. It is defined as the light flux emitted within a solid angle of one steradian by a source of one candela.
In practice, luminous flux helps determine the “amount” of light produced by a lamp or fixture, regardless of direction. For example, when comparing different lighting technologies, luminous flux (measured in lumens) provides insight into how much light each type of lamp generates.
Illuminance (Lux – lx)
Illuminance, formerly called illuminance, measures the amount of luminous flux incident on a surface. It is calculated by dividing luminous flux (in lumens) by the area of the surface (in square meters). One lux equals the illuminance on a one-square-meter surface receiving one lumen.
This quantity is vital for determining suitable lighting levels for environments such as offices, homes, or public spaces. Different activities require different levels of illuminance; for instance, a reading room requires higher lux levels than a corridor.
Luminance (cd/m² or Nit)
Luminance measures the amount of light emitted or reflected by a surface in a specific direction, expressed in candelas per square meter (cd/m²), or nit. It describes the apparent brightness of a surface to the human eye.
For example, a TV or computer monitor is characterized by luminance, which determines how bright the image appears to the viewer.
Luminous Efficacy (lm/W)
Luminous efficacy is the ratio of luminous flux emitted by a lamp to the electrical power consumed, expressed in lumens per watt (lm/W).
Higher luminous efficacy means more light is produced per watt of energy consumed, which is crucial for energy-efficient lighting designs. LEDs, for instance, offer high luminous efficacy, making them an energy-efficient choice compared to traditional incandescent bulbs.
Light Distribution Curve
The light distribution curve is a diagram illustrating how a fixture’s luminous intensity is distributed in different directions. Typically presented as a polar diagram, it shows intensities as a function of the angle formed with the vertical.
This diagram is essential for optimizing lighting placement and ensuring targeted illumination, such as in streetlights or floodlights.
Practical Applications in Lighting Design
Understanding these quantities is fundamental in lighting design practice, enabling precise calculations and efficient illumination planning. From selecting light fixtures to determining their placement, every decision affects visual comfort and energy consumption.
FAQ – Frequently Asked Questions about Lighting
1. What is wavelength, and how does it affect the color of light?
Wavelength is the distance between corresponding points on consecutive light waves. It determines the color of light, with shorter wavelengths producing violet light and longer wavelengths producing red light.
2. What is the difference between luminous intensity and luminous flux?
Luminous intensity (measured in candela) is the light emitted in a specific direction, while luminous flux (measured in lumens) is the total light emitted in all directions.
3. How is illuminance measured?
Illuminance is measured in lux, representing the luminous flux per square meter on a surface.
4. What is luminous efficacy, and why is it important?
Luminous efficacy (lm/W) is the ratio of light output to energy consumption. It indicates how efficiently a light source converts energy into visible light, essential for energy-saving designs.
5. What is a light distribution curve?
A light distribution curve shows how a fixture’s luminous intensity varies in different directions, aiding in optimal light placement for desired coverage.
If you liked this article, consider sharing it on social media, this will help to spread knowledge, leave your comment below so we can know your opinion.
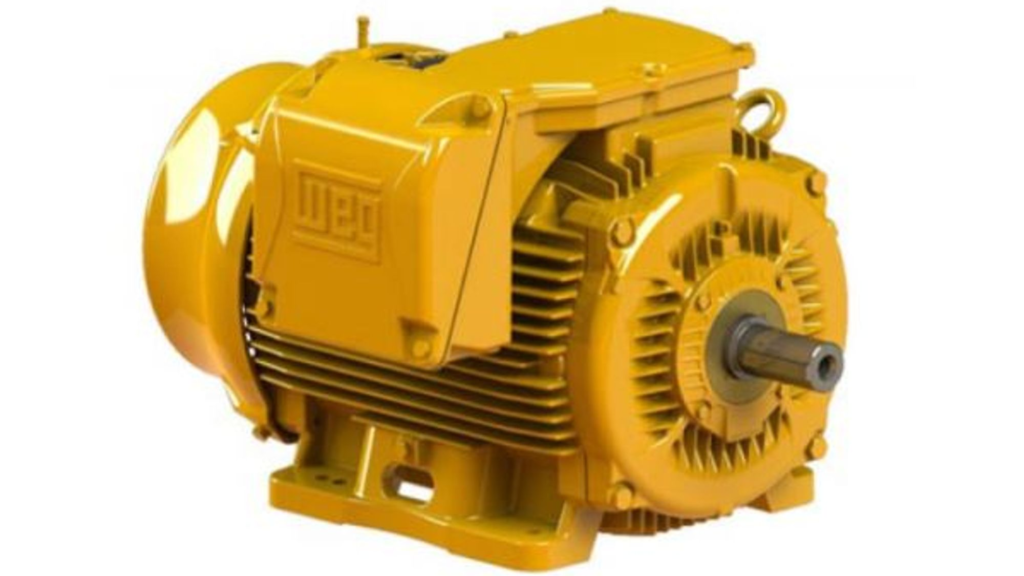
The insulation class of electric motors is critical for ensuring safe and efficient operation. It determines the maximum temperature a motor can withstand without compromising its lifespan, being directly influenced by the insulating materials used in the motor’s construction. In this article, we will explore the concept of insulation class, the importance of insulating materials, the most common insulation classes, and how to choose the most appropriate one for each application, based on standards such as IEC 60034-1 (International) and UL 1446 (USA).
What Is Insulation Class?
The insulation class of an electric motor refers to the ability of the insulating materials used in its construction to withstand the temperatures generated during operation. These materials are essential to prevent the deterioration of the motor’s internal components, protecting them from excessive heat that could cause electrical failures.
Insulating Materials
The insulating materials used in electric motors are designed to withstand high temperatures and harsh operational environments. The choice of insulation material is based on the maximum temperature it can handle without losing its properties. Some of the most common insulating materials include:
- Impregnated Paper: Mainly used in Class A motors, this material is impregnated with varnishes or resins to increase its thermal resistance.
- Synthetic Resins: Used in Class E and B motors, these resins offer good resistance to heat and moisture while providing effective electrical insulation.
- Glass Fibers: Used in Class F and H motors, glass fibers impregnated with special resins can withstand very high temperatures and are highly resistant to severe environmental conditions.
- Mica and Mica-Glass: Commonly applied in Class H motors, these materials provide excellent thermal and electrical resistance, making them ideal for environments with high thermal demands.
Each of these materials is selected based on the temperature the motor will experience during operation. The correct material choice ensures that the motor operates efficiently and without failure, even under extreme temperature conditions.
Importance of Insulation Class
Choosing the appropriate insulation class for an electric motor is essential to ensure it operates within safe thermal limits. Running a motor beyond its temperature limit can lead to the degradation of insulating materials, causing motor failures and necessitating repairs or replacement prematurely.
Insulation Classes and Their Temperature Limits
According to international standards like IEC 60034-1, insulation classes are categorized based on the maximum temperature the insulating materials can withstand. The most common classes are:
- Class A: Uses materials such as impregnated paper and varnishes, supporting temperatures up to 105°C (221°F).
- Class E: Uses synthetic resins with higher thermal resistance, supporting up to 120°C (248°F).
- Class B: Employs synthetic resins and combinations of mica, with resistance up to 130°C (266°F).
- Class F: Uses impregnated glass fibers and mica, supporting up to 155°C (311°F).
- Class H: Utilizes high thermal resistance materials like mica-glass, supporting up to 180°C (356°F).
Each of these classes has been developed to withstand different temperature levels, ensuring the motor functions efficiently in various operational conditions.
Most Common Insulation Classes in the Market
Among the various classes available, Class B and Class F are the most commonly used in the market. Motors manufactured with these classes use insulating materials that can withstand temperatures up to 130°C (266°F) and 155°C (311°F), respectively. The choice between these classes depends on the motor’s operating conditions, such as ambient temperature, load, and duty cycle.
How to Choose the Right Insulation Class?
Choosing the correct insulation class should consider several factors, including:
- Ambient Temperature: Motors operating in high-temperature environments require more resistant insulating materials, such as those used in Classes F and H.
- Load Conditions: Motors running under heavy load or with frequent start-stop cycles should have higher insulation classes to avoid overheating.
- Duty Cycle: For continuous or rapid load variation operations, Classes F and H offer the best protection against thermal wear.
For most industrial applications, Class B is sufficient. However, under more severe conditions or demanding duty cycles, Class F is recommended.
FAQ about Insulation Class in Electric Motors
- What is insulation class in electric motors?
- The insulation class defines the ability of insulating materials to withstand specific temperatures without losing their properties, ensuring the motor’s safety and longevity.
- The insulation class defines the ability of insulating materials to withstand specific temperatures without losing their properties, ensuring the motor’s safety and longevity.
- What is the difference between insulation classes B and F?
- The difference lies in the insulating materials and the temperature limits they can withstand. Class B uses synthetic resins, with resistance up to 130°C (266°F), while Class F uses impregnated glass fibers, with resistance up to 155°C (311°F).
- The difference lies in the insulating materials and the temperature limits they can withstand. Class B uses synthetic resins, with resistance up to 130°C (266°F), while Class F uses impregnated glass fibers, with resistance up to 155°C (311°F).
- How do I choose the right insulation class for my motor?
- The choice depends on ambient temperature, load conditions, and the motor’s duty cycle. For hotter environments or intense operations, a higher insulation class, such as Class F, is recommended.
- The choice depends on ambient temperature, load conditions, and the motor’s duty cycle. For hotter environments or intense operations, a higher insulation class, such as Class F, is recommended.
- What are the consequences of using a motor outside its insulation class?
- Operating a motor beyond its temperature limit can cause the degradation of insulating materials, resulting in electrical failures and a significant reduction in the motor’s lifespan.
- Operating a motor beyond its temperature limit can cause the degradation of insulating materials, resulting in electrical failures and a significant reduction in the motor’s lifespan.
- Do all electric motors have the same insulation class?
- No, motors are built with different insulation classes to meet various operating conditions. This allows them to be used in different types of environments and applications.
- No, motors are built with different insulation classes to meet various operating conditions. This allows them to be used in different types of environments and applications.
If you liked this article, consider sharing it on social media, this will help to spread knowledge, leave your comment below so we can know your opinion.
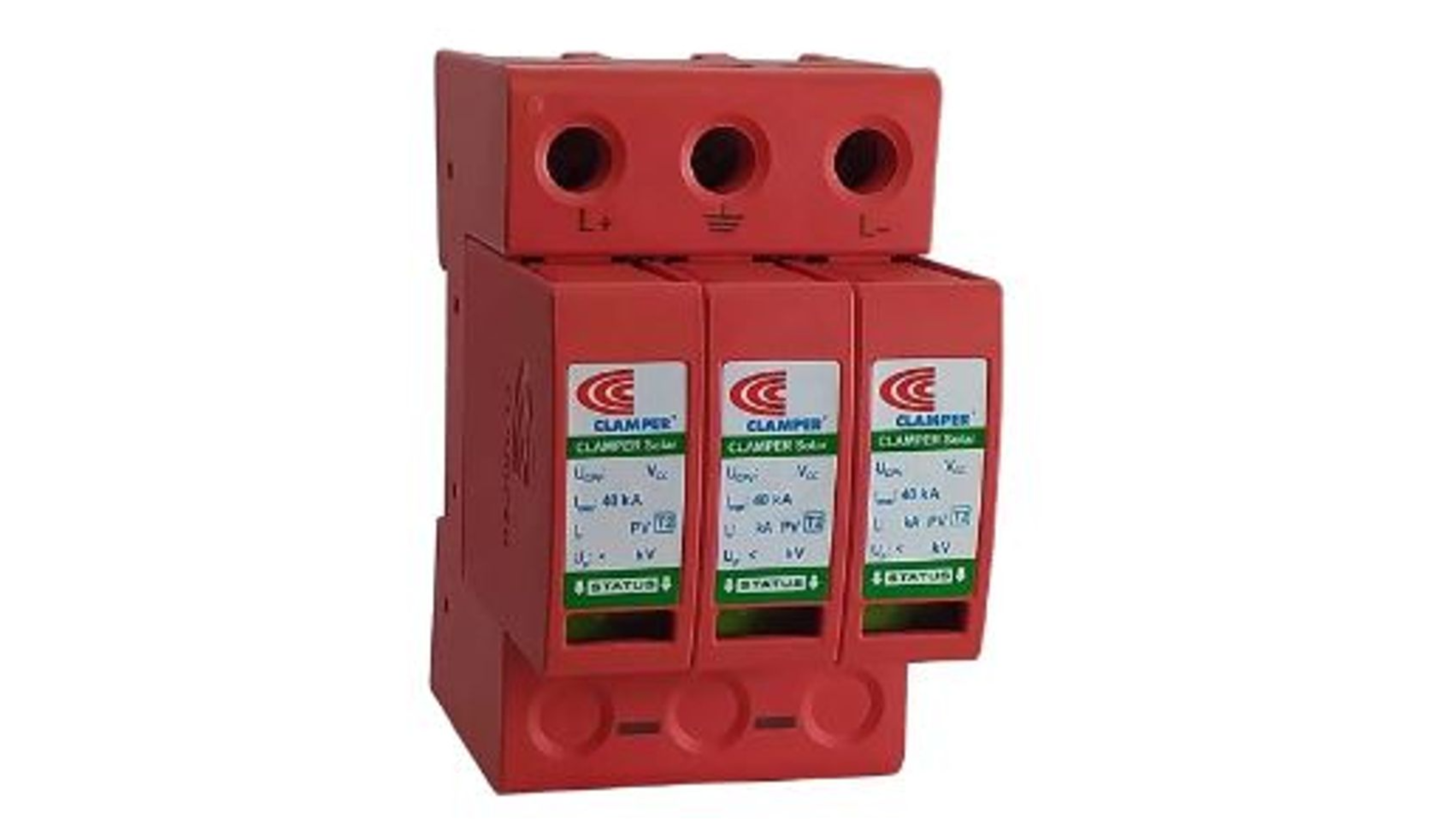
Surge protection in electrical installations is essential to ensure the safety and integrity of equipment and electrical systems. Surge Protection Devices (SPDs) play a crucial role in this process by diverting excessive energy caused by lightning strikes or other anomalies to the grounding system, thereby protecting the installation. This article provides a comprehensive guide to SPDs, covering their types, operation, relevant standards, and best installation practices.
What Are Surge Protection Devices (SPDs)?
SPDs are devices designed to protect electrical installations from voltage surges, which can be caused by phenomena such as lightning strikes or switching operations within the electrical network. These devices are connected between the phase and ground of the installation, diverting the surge to the grounding system and protecting the connected equipment.
Standards and Regulations
In the United States and the United Kingdom, the primary standard governing the installation and use of SPDs is the IEC 61643 series of international standards. These standards define guidelines for the protection of structures against lightning strikes and detail the requirements for SPD installation, including classification and positioning within the electrical system. For the UK, the BS EN 61643-11 is commonly referenced for low-voltage systems.
Classification of SPDs
SPDs are classified into different categories based on their capacity to withstand and dissipate surges:
- Type 1: Designed to protect against direct lightning strikes, these are robust and typically installed at the point of entry to the electrical installation.
- Type 2: Used for protection against indirect surges and switching overvoltages, they are frequently installed in distribution boards.
- Type 3: Provide additional protection and are installed close to sensitive equipment, such as electronic devices.
How SPDs Work
SPDs act as a kind of relief valve for excessive energy. Under normal conditions, they have high resistance, isolating the live conductors from the ground. When a surge occurs, the resistance of the SPD drops significantly, allowing the surge current to be diverted to the ground, preventing damage to equipment.
There are two main types of SPDs based on their electrical action:
- Short-circuiting: They abruptly reduce their resistance upon detecting a surge, directing it to the ground.
- Non-short-circuiting: They act as voltage limiters, gradually adjusting their impedance to divert the surge.
Types of SPDs by Technology
SPDs can be built using various technologies, each with specific characteristics:
- Spark Gaps: Use an electric arc to create a low-impedance path during a surge.
- Varistors: Resistors that change their resistance based on the applied voltage, they are quick and effective at dissipating surges.
- Suppression Diodes: Primarily used in Type 3 devices, these rely on Zener diodes to limit voltage.
Installation Topologies
The installation of SPDs must follow specific topologies, such as the TN-S and TN-C systems, to ensure the surge is effectively diverted to the ground. Additionally, it is common to use fuses in series with the SPD to add an extra layer of protection.
Lightning Protection Zones (LPZ)
Electrical installations are divided into Lightning Protection Zones (LPZ), which vary depending on the severity of the surges that may occur. SPDs are installed at the boundaries of these zones:
- Type 1: Between zones LPZ0B and LPZ1.
- Type 2: Between zones LPZ1 and LPZ2.
- Type 3: Between zones LPZ2 and LPZ3.
Best Practices for Installing SPDs
- Selecting the Right SPD: Choose the appropriate SPD based on the classification of the installation and the required levels of protection.
- Proper Installation: Follow standards such as IEC 61643 and ensure the SPD is correctly positioned and has effective grounding.
- Regular Maintenance: Regularly inspect SPDs, especially Type 3 devices, to ensure they are in good working condition.
FAQ about Surge Protection in Electrical Installations
- What is an SPD and why is it important? An SPD (Surge Protection Device) is a device that protects electrical installations from voltage surges by diverting excess energy to the ground. It is essential to prevent damage to equipment and avoid system failures.
- How do I choose the right SPD for my installation? The choice of SPD depends on the installation’s location, the type of protection needed (direct or indirect), and the sensitivity of the equipment to be protected. Refer to SPD classifications (Type 1, 2, 3) and standards such as IEC 61643 to make the correct choice.
- Where should SPDs be installed? SPDs should be installed at energy entry points, in distribution boards, and near sensitive equipment depending on the type of SPD. It is recommended to follow the TN-S or TN-C topology for optimal protection effectiveness.
- How often should SPDs be inspected? SPDs should be inspected regularly, especially after known surge events such as storms. Type 3 SPDs require more frequent checks, as failures in these may not be immediately noticeable.
- Can an SPD fail? Yes, SPDs can fail, especially after they have exhausted their energy dissipation capacity. It is crucial to monitor their condition and replace damaged units to maintain effective protection.
- What are the types of SPDs? SPDs can be classified as:
- Non-short-circuiting: Composed of nonlinear resistance-based or discharge-type arresters.
- Short-circuiting: Which directly act in a short circuit but are not recommended in all situations.
- Non-short-circuiting: Composed of nonlinear resistance-based or discharge-type arresters.
- When is the use of an SPD mandatory? The mandatory use of SPDs is specified by standards like IEC 62305 (and the corresponding parts in UK and US standards) in areas with a high incidence of lightning or where sensitive equipment must be protected.
- How should SPDs be connected to ground? The grounding terminal of SPDs should be connected to one of the following:
- A linked system including all metallic masses of the installation and any conductive elements outside the installation.
- An independent grounding electrode with appropriate resistance to handle fault currents.
- A linked system including all metallic masses of the installation and any conductive elements outside the installation.
- What precautions should be taken when connecting conductors to the SPD? The conductors connecting the SPD to the live conductors and the ground should:
- Be sized to handle the maximum currents that may pass through the SPD.
- Have cross-sectional areas according to protection conductor requirements.
- Be adequately insulated, equivalent to the installation conductors.
- Be sized to handle the maximum currents that may pass through the SPD.
- What is the difference between TN-C, TN-S, TT, and IT grounding systems? These systems refer to the configuration of neutral and protective conductors:
- TN-C: Neutral and protective conductors are combined into one conductor (PEN).
- TN-S: Neutral and protective conductors are separate.
- TT: Neutral and protective conductors are separately grounded.
- IT: Isolated ground system with a grounding point through high impedance.
- How do I choose the appropriate SPD for my installation? The selection of the correct SPD should consider nominal current, maximum residual voltage, and the required protection level. It is also important to take into account environmental conditions, such as exposure to lightning, to determine the need for a higher current capacity SPD.
- Why is installing SPDs in a building important? Installing SPDs is crucial for protecting electrical and electronic equipment from damage caused by transient overvoltages. This enhances the safety of the installation, prevents financial losses due to equipment failures, and ensures the continuous operation of critical systems.
If you liked this article, consider sharing it on social media, this will help to spread knowledge, leave your comment below so we can know your opinion.